
This can nearly eliminate a company's investment in raw materials inventory. This approach requires a business to use the services of a cluster of highly-efficient local suppliers. Instead, a company requires its suppliers to submit to a quality certification process (so that it can avoid any time-consuming receiving inspections), and then has them make a large number of small deliveries, sometimes directly to wherever the parts are needed in the production process. In fact, there may be no on-site inventory at all. Quicker Raw Material DeliveriesĪ JIT system does not require a massive amount of on-site inventory. This, in turn, reduces the amount of work-in-process inventory traveling between the work stations. In addition, management is more likely to move the workstations closer together, to reduce the amount of travel time on the conveyors. This eliminates a great deal of material handling personnel and equipment. When inventory lot sizes are so small (as just noted), it makes more sense to place them in very small transport containers and move them to the next workstation by a conveyor belt. This, in turn, tends to reduce inventory levels, since there is no longer a need to spread the cost of a machine setup over a very long production run. By doing so, it becomes cost-effective to rapidly re-set a machine to manufacture even a single unit. Consequently, there are a number of tools and concepts available for greatly shortening machine setup times.


JIT advocates small lot sizes, but this is impossible when it takes a long time to set up a machine for each production run. This immediate feedback loop greatly limits the amount of scrap generated within the production system. As each lot is completed, it is immediately passed along to the next downstream workstation, where the production staff inspects it, and can reject it at once if quality standards are not met. This means that inventory moves through the production process in very small, discrete batches.
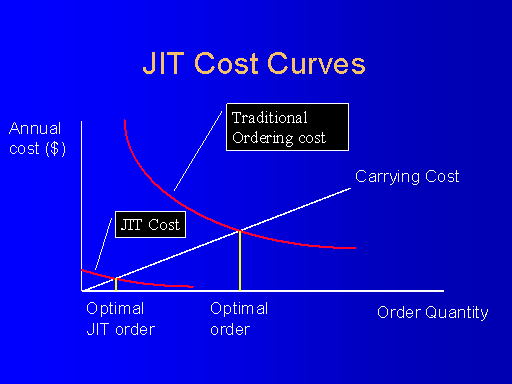
Wherever possible, JIT advocates very small production lot sizes, preferably of just one unit. By comparison, a traditional push manufacturing system runs work orders through the production system that are based on forecasts, and which typically result in much larger quantities of inventory in the production system at any given time. Thus, the pull concept massively reduces the amount of work-in-process inventory. If the downstream workstation issues no kanban, then the workstation will remain idle until notified. A workstation is only allowed to produce the exact amount of the authorization. Under JIT, each step in the production process is triggered by a notification, or kanban, that is provided to it by the downstream workstation that is a request for a specific quantity of an item. Just-in-time inventory control involves implementation of the following concepts: The Pull Concept This control system does so by pulling demand through a production facility, where each step in the production process is only authorized to produce a limited amount of inventory.
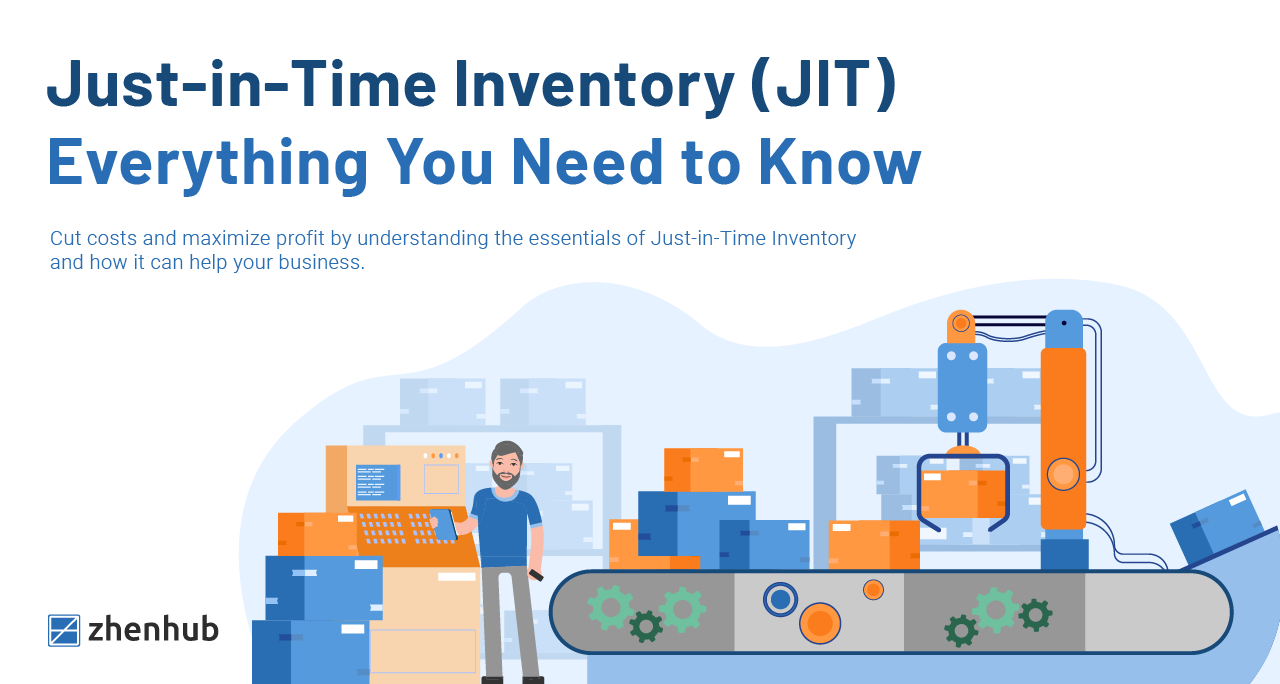
The concept is based on a cluster of lean manufacturing activities that are designed to only manufacture enough products to meet customer demand. Just-in-time (JIT) inventory control reduces the amount of inventory that a company maintains.
